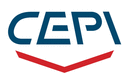
Cepi Spa
About Us
Cepi designs, manufactures and installs turn-key systems for the storage, conveying and metering of raw materials, as well as fully integrated automation and technologies to complete all production processes. Since 1985, we built more than 10.000 installations the world over, working with the most important companies in every market of the food industry.
CEPI is based in the Emilia Romagna region in Italy and operates globally, with offices in Malaysia to coordinate operations in the Asian market. We take care of every aspect of the project: process and product analysis with hygiene and safety management, engineering and control, direct manufacture of all machinery and components, project management, logistics, installation, commissioning and customer service (remote and local support, repairs, spares, maintenance, testing and training.)
Our offer includes indoor and outdoor storing of powders, granular products and liquids, clean and energy efficient conveyance systems, dosing on multiple lines in hoppers, blenders and tanks for liquids, integrated automation of operations and full traceability. We can also fit your installation with applications such as fermentation, flour cooling, fluidization, sugar milling, invert sugar, salt solution, cold fat dosing and scrap rework. Our motto is: if a process needs it, we can do it. If we can't do it yet, we will.
We provide an an automated management of the dosing process that ensures efficiency, achieves a final product of high quality and unique flavor, and easily accomodates future expansion due to the flexibility of the process. Our automatic installations provide precise and repeatable recipes, higher production volumes, traceability of materials and processes, enhanced communication with other software and ERP, higher hygiene, reduced consumptions and pollution.
We build lasting relationships for lasting projects, through an ongoing conversation which concerns all its aspects. A network of local partners spanning the five continents, able to provide technological and sales related support at all stages of the project. With fully customized solutions ensuring continuity through all operations and all encompassing support, we dedicate each project the care it deserves.
Our values
Our vision prioritizes flexibility, research, and customization. Our product is the installation rather than any specific machine, and our best-selling service is customization. Our technologies adapt and evolve to match the demands from the manufacturer side, leading to unparalleled technological range.
Our mission is twofold: to build specialized turn-key installations that manage the entire production line from storage to dosing, and to develop customized technological solutions to match diverse and ever evolving needs across the planet. We bring to the table a global knowledge of materials, environments and markets as well as the continued research that goes into developing around 300 unique systems every year.
Expertise, teamwork, communication and interconnection. All our teams are highly qualified, combining expertise and experience with an orientation to innovating, as well as an ease in integrating other resources. A team of 21 engineers and 24 automation programmers develop the mechanical and automation systems in parallel, and all our projects are designed with a deep knowledge of the materials and a special commitment to hygiene and safety. Food technology expertise guarantees a perfect match of our system with your raw materials, and is at your disposal during the development of recipe, assisting with your own research and innovation. Our Quality Control department will monitor all processes to confirm compliance with regulations and the hygiene and safety of all equipment.
All our processes have been certified to Occupational Health and Safety standard UNI ISO 45001. Our equipment is compliant with ATEX directive 2014/34/UE, Machinery Directive 2006/42/CE and all international legislation for articles intended for contact with food. Our equipment is manufactured in a channeled system certified to international standard UNI EN 1090.
Fragrance, taste and integrity: with vaste food technology expertise, all our technologies are designed factoring the preservation of flavour
and ingredient properties.We developed special materials and manufacturing techniques to protect the raw materials, such as antistatic fabric Trevira for indoor silos, and exclusive key-hole welding techniques to prevent residuals and pollution.
We employ an exclusive welding technique to prevent pollution in stainless steel equipment, and antistatic HT Trevira fabric in our fabric silos, with patented technology to ensure equipotentiality. We provide multiple ATEX conform systems to prevent and contain explosions, flames and contamination, as well as filtering systems and other air treatement solutions.
Our technologies and installations are designed to minimize energy consumption, material consumption and waste, with an individual analysis of energetic impact. Machinery and piping are in stainless steel with a long life cycle, and our storing equipment allows for chronological extraction, which greatly enhances waste efficiency. Our production chain is as green as can be with direct manufacture in our factory in Italy and mostly local suppliers. Our new home will be powered and heated by renewable energy.