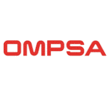
OMPSA S.r.l.
Who we are
The OMPSA mechanical workshop was founded after the Second World War when it started manufacturing industrial machinery, then, in the 1960s, the company began to design and build mechanical presses for stamping and cutting small metal parts for the footwear sector..
Today the production comprises 4 column eccentric presses, (with 25, 40, 50, 63 and 85 tons), 2 column eccentric presses (with 25, and 40 tons), double knuckle-joint eccentric presses (with 25, 45, and 75 tons) and related accessories.
These machines are employed in all those applications which use progressive working dies and require high precision and medium to high production speed.
Four column double knuckle-joint presses are employed for work which requires precision pressing and coining.
The 4 column driving system and the double knuckle-joint guarantee high precision in parallel lowering, noise reduction, both during pressing and shearing.
Ompsa can supply complete plants for the pressing of small metal piecework.
Today our products are shipped all over the world: we have gained experience in the small metal parts sector relating to the fashion field (clothing and footwear), electrical and electronic sectors (faston, cable lugs, connectors, contacts,..), automotive, small components for the household appliance sector and in general all those sectors that produce small metal parts and that use progressive dies starting from metal strip at medium-high production speeds.
Ompsa presses are sold all over the world, our assistance network guarantees an excellent and rapid after-sales service.
Our values
We firmly believe that our products must always keep pace with the technology offered by the market. For this reason, we always listen to the needs and requests of our customers, which make our growth and technological development possible.
We believe that safety is the top priority in our machines: their reliability guarantees precise processing, necessary for the production of high-quality components. The possibility of interconnecting our machines makes remote control and monitoring possible. Thanks to these intelligent technologies, technicians can quickly diagnose any problems, reducing downtime and optimizing production.
Remote intervention allows us to solve problems without the need to travel, reducing additional costs related to technicians and vehicles, to the benefit of the environment around us.